Plastic extrusion for tubing, profiles, and custom shapes
Plastic extrusion for tubing, profiles, and custom shapes
Blog Article
Comprehending the Basics and Applications of Plastic Extrusion in Modern Manufacturing
In the world of modern manufacturing, the method of plastic extrusion plays a critical duty - plastic extrusion. This complex procedure, including the melting and shaping of plastic via specialized passes away, is leveraged across different industries for the development of diverse products. From auto components to durable goods product packaging, the applications are substantial, and the potential for sustainability is just as impressive. Untangling the fundamentals of this process discloses truth flexibility and capacity of plastic extrusion.
The Basics of Plastic Extrusion Refine
While it might appear complex, the principles of the plastic extrusion process are based on fairly simple concepts. It is a production procedure wherein plastic is melted and after that shaped right into a continual profile through a die. The plastic extrusion procedure is thoroughly utilized in different sectors due to its adaptability, efficiency, and cost-effectiveness.
Various Kinds Of Plastic Extrusion Strategies
Structure upon the standard understanding of the plastic extrusion procedure, it is essential to explore the numerous strategies included in this production approach. In contrast, sheet extrusion creates large, flat sheets of plastic, which are normally additional processed into products such as food product packaging, shower curtains, and cars and truck components. Understanding these techniques is key to making use of plastic extrusion effectively in modern-day production.
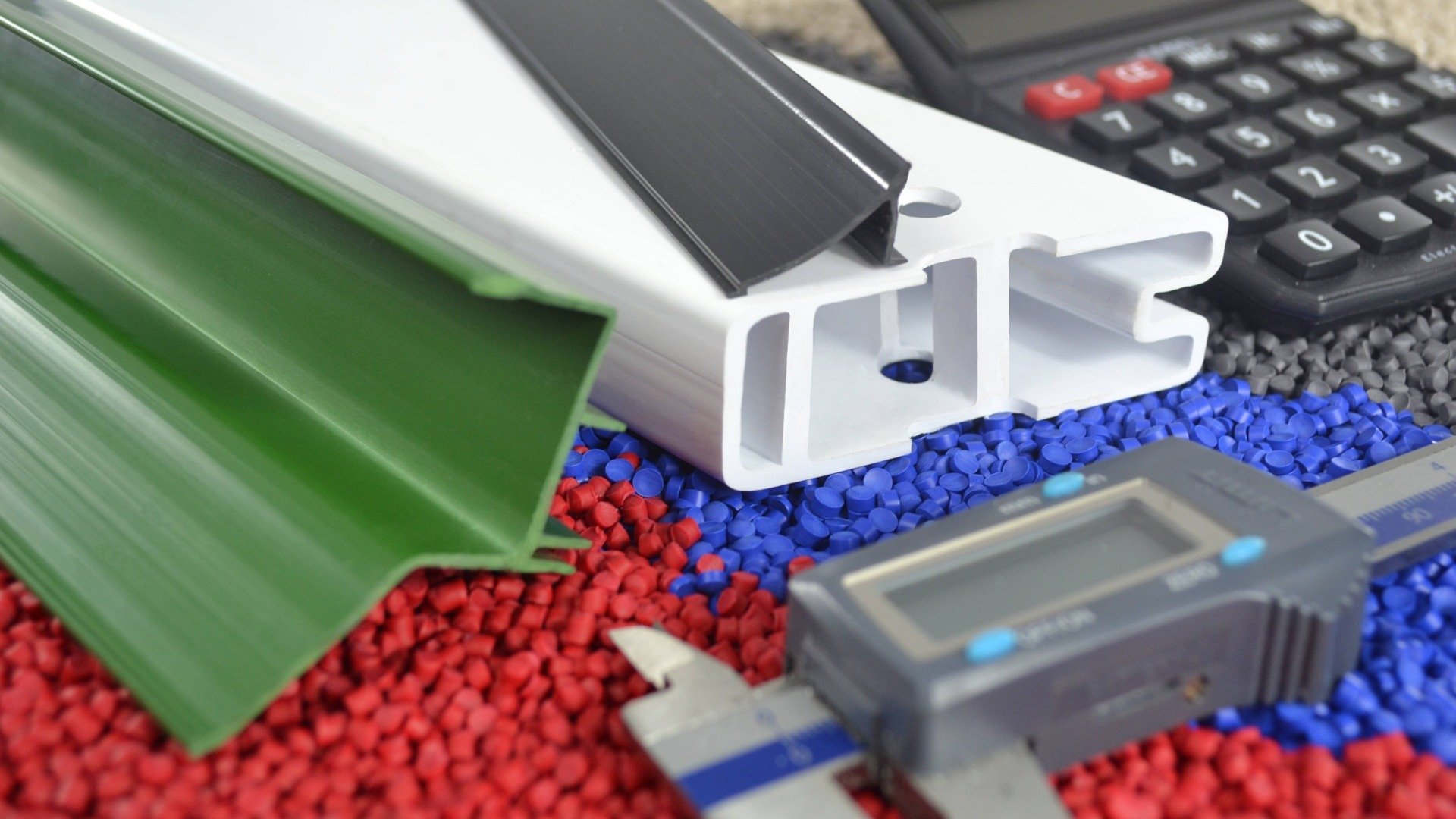
The Duty of Plastic Extrusion in the Automotive Sector
A frustrating majority of parts in modern-day lorries are items of the plastic extrusion process. This procedure has actually reinvented the automobile industry, changing it into a much more effective, affordable, and versatile manufacturing sector. Plastic extrusion is largely utilized in the manufacturing of various auto elements such as bumpers, grills, door panels, and dashboard trim. The procedure provides an uniform, consistent result, allowing suppliers to create high-volume get rid of great accuracy and minimal waste. The agility of the extruded plastic parts adds to the total reduction in car weight, boosting fuel efficiency. The toughness and read what he said resistance of these parts to warmth, cool, and impact enhance the durability of automobiles. Therefore, plastic extrusion plays a critical duty in auto manufacturing.

Applications of Plastic Extrusion in Durable Goods Manufacturing
Beyond its significant effect on the automotive industry, plastic extrusion confirms similarly reliable in the realm of customer goods manufacturing. This procedure is critical in creating a broad range of products, from food packaging to household home appliances, toys, and also medical devices. The versatility of plastic extrusion enables makers to create and create complex sizes and shapes with high precision and performance. Due to the recyclability of lots of plastics, extruded parts can be reprocessed, lowering waste and expense (plastic extrusion). The flexibility, flexibility, and cost-effectiveness of plastic extrusion make it a recommended option for several durable goods makers, contributing significantly to the sector's growth and innovation. However, the ecological implications of this widespread usage require mindful consideration, a subject to be gone over even more in the succeeding section.
Ecological Influence and Sustainability in Plastic Extrusion
The pervasive usage of plastic extrusion in producing welcomes scrutiny of its ecological ramifications. Reliable equipment lowers energy use, while waste monitoring systems recycle scrap plastic, decreasing raw product needs. In spite link of these renovations, better innovation is needed to mitigate the environmental footprint of plastic extrusion.
Final thought
Finally, plastic extrusion plays a crucial duty in modern production, especially in the automotive and customer items fields. Its adaptability permits the production of a large range of parts with high accuracy. In addition, its potential for reusing and growth of naturally degradable products provides a promising method towards lasting methods, consequently attending to ecological problems. Recognizing the basics of this procedure is essential to enhancing its advantages and applications.
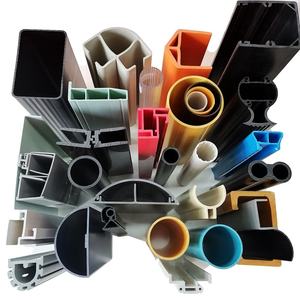
The plastic extrusion procedure is thoroughly utilized in different markets due to its convenience, efficiency, and cost-effectiveness.
Building upon the standard understanding of the plastic extrusion procedure, it is needed to check out the various strategies entailed in this manufacturing method. plastic extrusion. In comparison, sheet extrusion produces big, flat find this sheets of plastic, which are typically more processed into items such as food packaging, shower drapes, and cars and truck parts.An overwhelming bulk of parts in modern automobiles are products of the plastic extrusion procedure
Report this page